Hello everyone! Here is my design preview for my final project for the Aesthetics in Design class.
For this project, I am making a 3D printed performance running shoe midsole, with a reach goal of building out the whole shoe with an upper and lacing. While some companies have made shoes like this, they are normally expensive, not durable, and do not serve as good running shoes.
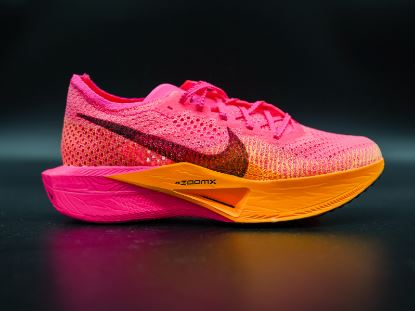
Shoe technology has created a craze in the performance running industry recently; new innovations such as light and responsive foams and carbon fiber plates have given these shoes performance-enhancing ability. These new running shoes can sometimes even increase a runner’s biomechanical efficiency by up to 4%, therefore increasing runners’ performance in competition. Nearly every running shoe company has now produced their own version of a “Super-Shoe” to help their customers run faster. These shoes are typically priced at a massive premium, and customers are more than willing to pay it for their amazing effects on running performance. Now, large shoe companies are starting to shift their focus to making these technologies sustainable.
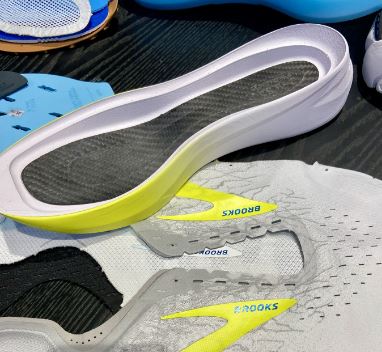
Foam is a very difficult material to recycle, and cannot be easily converted back into its original plastic. Because of this, used shoes either have one useful life, or are turned into low quality recycled foam products. Now, with shoes being made with lighter and less durable foam to increase performance, this problem is bigger than ever.
An additional factor in this problem is the premium that is charged for these foam shoes that are not durable. In theory for the running companies, this is a near-perfect business model. The company makes a better shoe that breaks down almost twice as fast as standard running shoes, and charges about 50% more for said running shoes. That multiplies revenue by about four times! The sad part is that the customer now also pays four times the amount of money for their shoes.
There have been a few proposed solutions to this problem. Adidas was the first company to release a 3D printed midsole on a running shoe, a disruptive innovation in the shoe industry. Interestingly enough, Adidas outsourced this idea to an additive manufacturing company, Carbon 3D, that specializes in creating surrogate foam out of 3D printed lattice structures. This company also works on bike seats, impact cushioning in helmets, and many other applications. These companies helped to give me the inspiration for creating a 3D printed midsole that has a futuristic aesthetic.
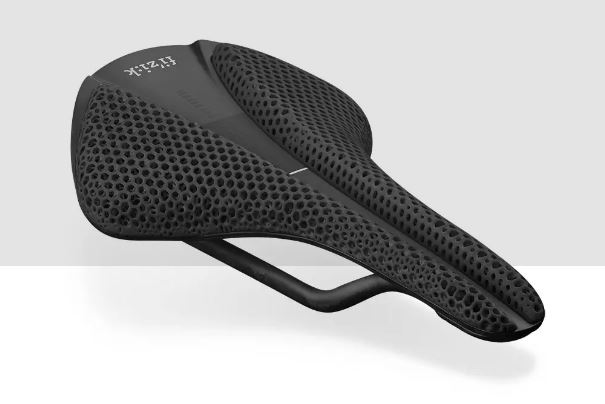
A few companies have also tried to attack the problem of recyclability. Nike and On Running have both created shoes that aim to mitigate waste after the shoe’s useful life. Nike has worked on multiple lines of running and casual shoes that feature recycled material as the primary component of the midsole. These include modified versions of the Pegasus Turbo, the Space Hippie Series, and multiple Air Max spinoffs. On Running has recently published a series of shoes and apparel under the name Cyclon. This series aims to create products from one natural material, castor bean oil. From this oil, On Running has created a fully-fledged shoe and performance training shirt through many manufacturing processes. Both of these products are specifically designed to be recycled. From these two companies, I found that if I were to make my own version of a running shoe, I would want it to be recyclable for at least two useful lives.
Lastly, a few companies have tried to release performance running shoes at an affordable price. While many companies offer cheap, budget running shoes, these are never up to par in comfort and performance with what the companies can really do. The primary affordable running shoe company right now is called Atreyu Running. This company offers a simple and stripped-down version of reliable running shoes. They offer an elite running shoe for only $120, while the going rate for similar shoes at other companies is about $250. This has been an interesting business to follow because they are a startup in Texas that works diligently to reduce waste and losses in their supply chain and business structure so that they can maintain this low price. This is a very interesting strategy to me, and while Atreyu Running does a good job at selling affordable shoes that function well, they still go about it in a very standard way. Their shoes all play by the same rules as the massive shoe companies, and so it is difficult to achieve the prices they have. Atreyu’s story is what gave me inspiration to make this shoe as affordable as possible in production.
My project would create an easy, affordable, durable, and recyclable running shoe that can hopefully match the performance of $250 elite running shoes for just a fraction of the price! Because I am using additive manufacturing, I do not have to pay for the expensive foaming processes used by major running shoe companies. Based on the research, results, and products released by Carbon 3D, I can achieve equivalent properties of foam by using 3D printed plastic. Also, 3D printed plastic is known to be recyclable, because as thermoplastics, they can be melted down, filtered, and reused. Finally, all of these processes are achievable with what is available at the Idea Forge at CU Boulder, making it a would-be “most affordable elite running shoe of all time.” The thing that sets my shoe apart is that it achieves all of the qualities that the above solutions solve one of each.
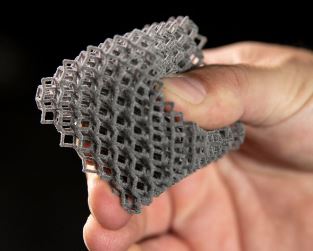
For this design, I will use TPU plastic, provided by the Idea Forge, which will be printed on the FDM printer. TPU plastic is known in the running industry to have good elastic properties, and is widely available. With the 3D printing plastic, it is known that it is generally difficult to get completely isotropic properties with standard infill patterns. Because of this, I communicated with Pat MacGuire at the Idea Forge about infill patterns, and found that I am able to print components with a gyroid infill. Gyroid infill is a unique pattern that provides nearly isotropic properties for the part. Being isotropic, the gyroid infill can be printed with no outer shell layers on the print, revealing the inner pattern. Another cool aspect of gyroid infill is that it has a very organic pattern and look, which adds to the aesthetic of futuristic and organic, complementing the recyclable and affordable nature of this design.
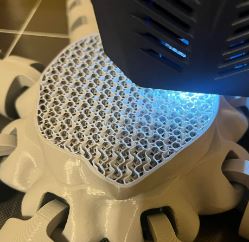
My goal in this project is to create a whole shoe, upper, midsole, and outsole, with either 3D printed or purchased materials. As mentioned above, I will make the midsole out of TPU, but the jury is still out on the upper and outsole. I do plan to buy insoles from SuperFeet, which provide form fitting and comfortable insoles. I also will buy shoe laces from a local running store. For the outsole, I will either use the same TPU material with a 100% infill, or some sort of used rubber to recycle it. To attach all of the components, I will use an epoxy adhesive to connect them in a durable way. In the event that I cannot construct a serviceable upper, I can also use one of my old running shoes as a prototype upper. This would obviously be a downgrade from the potential of the finished product, but the midsole is the primary functional and artistic innovation of the project, and so an incompletion of the upper or outsole would not really be considered a project failure, as long as the midsole achieves the goal aesthetic and function.
For the moving components of the design project, the midsole of the shoe will be a compressible component, but I have also heavily considered adding a slot in the midsole in which I could add a stiff plate with high flexural strength that resembles a carbon fiber plate, as is seen in many elite performance running shoes. Luckily, the Idea Forge can 3D print fiberglass-infused material on the MarkForged 3D printers, which resembles an affordable version of carbon fiber, which consists of fiberglass, carbon, and epoxy. In this way, I can produce an affordable equivalent of carbon fiber that can be inserted into the shoe’s midsole. A more flexible shoe without a plate is desirable for an easy run, but a stiffer shoe with higher rebound is desirable for a faster workout, so I could produce both types of shoes.
My goal aesthetic in this project is a futuristic and organic design. This aesthetic primarily relies on the nature of a gyroid infill in the midsole, which will be clearly shown in the midsole, which will have zero outer shell layers. The aesthetic is also achieved by the inherent recyclability of the shoe, which would deem the shoe a “shoe of the future” and an “affordable alternative” to modern running shoes. In the event that the midsole collapses too easily, compromising the structural integrity of the shoe, I will add shell layers to the midsole print to add support to the shoe. The problem with this is that it would completely change the design aesthetic of the shoe, from futuristic and organic to sleek and minimalist. This would still achieve the goal of the project, but it would drastically change the visual appeal of the product.
I am excited to see how this project turns out, and I will keep the site updated as I progress!
Inspirations and references
Adidas 3d printed shoe
https://www.adidas.com/us/4dfwd-3-running-shoes/IG8987.html
Carbon 3d
https://www.carbon3d.com/
Nike Running Shoes
https://www.nike.com/t/pegasus-turbo-next-nature-mens-road-running-shoes-pnz45r/DM3413-005?nikemt=true&cp=98549970627_search_–x-20451925136—c—–9028820-1012323799-00196607685877&gad_source=1&gclid=Cj0KCQjwncWvBhD_ARIsAEb2HW_gaWrzSbnxph90qqclideD1jT6P3rEJ5qiIU-ucLDeNsF2kbV4FbIaAlLwEALw_wcB&gclsrc=aw.ds
On Running Shoes
https://www.on.com/en-us/collection/cyclon
Atreyu Running Shoes
All Products – Running Shoes and Gear
My own WRTG3030 Report from Fall 2023
https://docs.google.com/document/d/15rvlY4FPWBz7m3AgOdxXLQyAZWPiU0vXIdYzBSpIiJU/edit?usp=sharing
2 Comments. Leave new
Hey Jace, I like your idea ! and your report tells a compelling a comprehensive and well-researched design preview for their final project, demonstrating a deep understanding of the running shoe industry’s challenges and potential solutions. The incorporation of sustainable materials, additive manufacturing techniques, and innovative design elements reflects a thoughtful approach to creating an affordable and functional performance running shoe. Could you provide us with more insight into how you plan to address potential challenges related to the durability and performance of the 3D printed midsole, especially in comparison to traditional foam midsoles?
Hi Aryan!
Thank you for the feedback! But in response to your question, it will definitely require a lot of testing. So far in the project, I have made multiple 3″x2″x1″ blocks of TPU with gyroid infill at the Idea Forge, each with a different infill density. By comparing these blocks with modern shoe foams, I hope to choose an infill density that can accurately model a foam underfoot. Durability will be something to test over time, but I do know that gyroid infill is one of the strongest infills before plastic deformation in 3D prints, and TPU itself has mild elastic properties!