Hello everyone, I am designing a 3D printed shoe for performance running. My goal is to be able to print all of the components of the shoe, with the exception of the insole, laces, and outsole, which are all generally easy to acquire or make. I am a runner, and the running shoe industry typically has prices that are through the roof for shoes that do not last very long, and are not easily recycled due to the foam used.
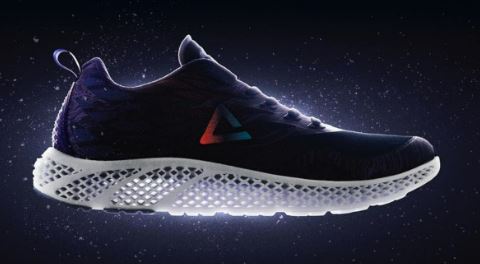
For the midsole, I am going to design a silhouette of a performance shoe’s midsole, based on a current popular running shoe model. I will then submit it to the Idea Forge for fabrication. I will request a gyroid infill for slicing, and the number of shells will depend on the aesthetic that I aim for.
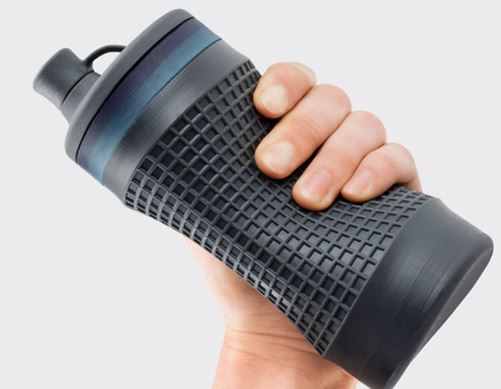
I plan to use a TPU filament for the midsole due to its natural rebound abilities, and the infill is something that I will have to test before printing the full part. Some elite shoes have a durometer rating of about C32, which converts to A66, so I can use a durometer to test the viability of my print as a surrogate foam.
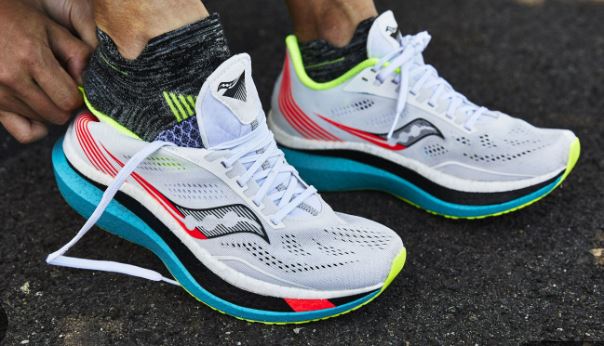
In the event that the midsole fails, I will have to do some intense research on the best possible material and infill pattern, and make decisions on how to proceed from there. The midsole is really the primary innovation of this design, and so it is the one I am really counting on to work well.
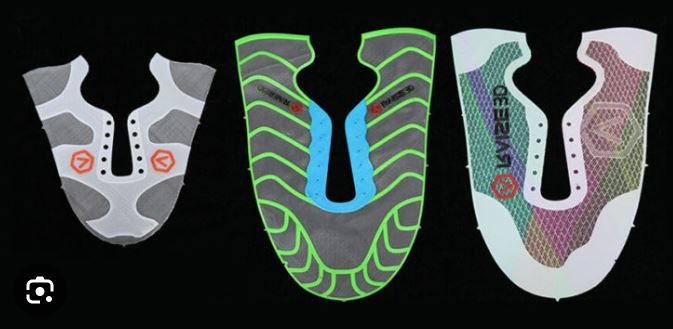
For the upper, I plan to print a thin mesh designed as a flattened geometry, with increased support in high impact and corrosion places. This is generally better than a print that is already in a shoe’s geometry because I will also include on this geometry an extra tab to use adhesive or sew to attach the upper to the rest of the shoe. Failure of the upper is less concerning to me than a failure in the midsole. If I am unable to get the correct geometry of the shoe’s upper, I can use one of my running shoes, take of the midsole, and utilize that shoe’s upper on my new midsole. While this will heavily impact the design aesthetic of the shoe, my primary goal in this project is to make a functional midsole for a performance running shoe.
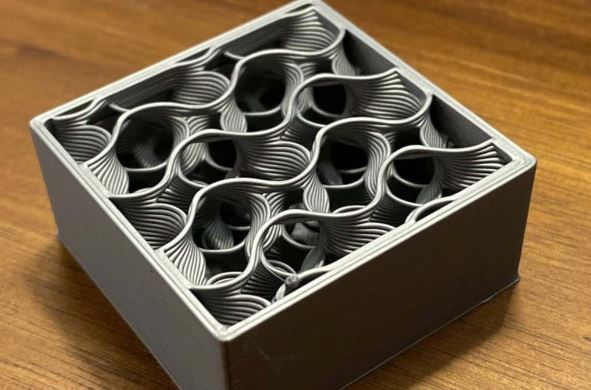
The goal design aesthetic of this project is a combination of organic and futuristic styles. These will both be achieved in the midsole if all goes to plan. a gyroid infill has a naturalistic appearance, and its presence in the shoe gives a sense of something new, unusual, or futuristic. In the event that the infill does not go as planned, I will have to add shelled walls to the midsole. The upper will also help the futuristic design of the part if it all comes together well. Outside of the appearance alone, 3D printing filament can usually be recycled, or can be composed of recycled material. This is something that would be greatly needed in the shoe industry, which is known for causing inordinate waste by using foam.
Thank you for reading!
Sources:
chrome-extension://efaidnbmnnnibpcajpcglclefindmkaj/http://www.fastenernetwork.co.uk/upload/docs/hardnessconversiontablepdf.pdf
4 Comments. Leave new
Hey Jace, thanks for a clear understanding of the problem you aim to solve with your project, highlighting the issues with traditional running shoe manufacturing and the need for sustainable alternatives. The detailed explanation of the design process, including material selection and infill testing, showcases a well-thought-out approach to creating a functional and innovative running shoe.Just out of curiosity, could you provide more insight into how the combination of organic and futuristic styles will be reflected in the final design of the shoe?
Hi Aryan,
Thank you for the response! And I’m sorry about the mild explanation of how the aesthetics will be implemented!
The awesome part of a gyroid infill is that it is nearly isotropic, meaning that the infill alone can sustain loads in any direction. Because of this, gyroid infilled parts can actually function without any shell walls! With no shells, the organic gyroid infill (pictured in the article) can be fully exposed in the midsole of the shoe, giving the midsole a very organic pattern to viewers.
The futuristic aesthetic is something that can come across in the upper of the shoe, and in the somewhat absurd gyroid in the midsole. It is something very unexpected and not normally seen, and so it will help to throw viewers off, and feel that it is something new and exciting, especially if it works well!
Hi Jace, I think your project is so cool and really unique. Have you ever tried printing with the filament you plan on using before? I was just curious how it works and how comfortable it will be as a running shoe sole.
Hi Kyra!
The filament I plan on using for this project is TPU with a 95A Shore Hardness. It will be printed on a FDM printer in the Idea Forge. While I haven’t printed with this filament before, TPU is a known and reliable foam in the running shoe industry, and so I trust its mechanical properties.
Running shoes are typically much softer than this (about 65A), which is why the infill density is critical to the success of this project.
If I had infinite time and resources, I would definitely search for a filament or resin with mechanical properties that surpass TPU, such as Loctite 3D IND402 Elastomer resin, which is one that I found to be perfect for a shoe midsole, but not compatible with any printers available to me.