An important part of the creative process is to identify specifications and potential constraints. This can allow engineers and designers to help benchmark their designs and begin to work around areas that could hamper the process. For my project specifically, since it is a bit ambitious for the amount of time available, I wanted to lay out the constraints to find ways to work around them while staying true to the specifications that I want the project to meet. From the project inception, I wanted to gain experience with mechanical design while also being able to focus on the aesthetics of the project. As such, I have several specifications that I want my project to be able to meet to satisfy both of my initial vague goals. A large source of inspiration have been the organic-motion kinetic sculptures by Derek Hugger.
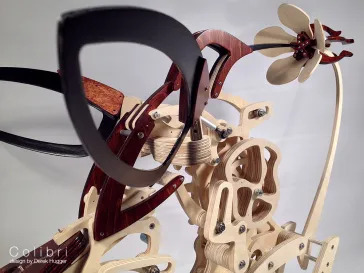
Specifications
My top specification is that the project must be able to convert potential energy to kinetic energy. My initial plans have this occurring using an escapement mechanism, but another controlled release of energy to drive a dynamic sculpture would be acceptable as well. Since the project must be dynamic, at least to some extent, this specification seems the most important from a requirements perspective. However, beyond that, my own personal goals for this project mean that being able to convert potential energy into kinetic energy through the use of a variety of mechanisms is a crucial benchmark for success. While I am not overly concerned that this is possible and feasible, it is an important part of my definition of success for this project.
In addition to functionality, the project must conform to the aesthetic of wooden kinetic sculptures and antique clock mechanisms. This includes a focus on the geared mechanism, and from the wooden kinetic sculptures, accents with different types of wood or different stains. This helps create contrast. I particularly want to focus on forms of ornamentation because I often neglect form in favor of function for my other project.


The overall aesthetic of the product should look clean, finished, and consistent. The final artifact shouldn’t appear “cheap” but instead should be well made. I would like to have a piece that looks polished enough and functions well enough to act as a display or portfolio piece. To this end, there shouldn’t be any extraneous machining marks, obvious joinery marks, or poor surface finishes. Unfinished sections are acceptable as they fall within the aforementioned aesthetic, but they should appear intentionally unfinished.
The mechanism shouldn’t be overly large or small. While I don’t have exact size constraints the mechanism shouldn’t be smaller than 8″ or larger than 24.” This is because I want to be able to easily display the mechanism either on a desk or by hanging it from a wall. If the final product is too large or small this could become difficult or it could be hard to appreciate from a distance.
Finally, while not a functional or aesthetic requirement, I want the project to be relatively easy to manufacture. That is because I am anticipating needing to spend a large amount of time working on the design and assembly. If the manufacturing is relatively easily, I will have more time to spend on the design and aesthetics.
Constraints
First and foremost amongst the constraints I am worried about time. There isn’t a lot of time left in the semester before the final project is due. Additionally, I anticipate needing to spend a lot of time working on a CAD model before I can even begin to manufacture or assembly it. All of this will take a considerable amount of time and I am worried that between this and other project, I will be stretched thin.
I am also worried about my ability to design the mechanism. I don’t have much mechanical design experience, and I worry that the project necessitates a large degree of complexity which may stretch my skills as a designer. While I am excited for the challenge, the intricate gear and cam mechanisms typical of my chosen aesthetics will present a large challenge.
Another constraint for this project is cost and the ability to access different materials. While I am fairly certain that the bulk materials for the project will be readily available, since I want to use different woods for accents I may find difficulties in procuring materials that can be used with my chosen manufacturing processes. Additionally, the cost of these materials could potentially be prohibitive in the design that I want to achieve.
Another constraint I must keep in mind will be the connection between the gears and their rods. Depending on the direction I go in, this could be a large constraint as there may need to be a mechanical connection between the two. This could be challenging as I am planning on using laser cut wood and brass for the axles.
Finally, I may be constrained by my manufacturing processes. I am planning on papercutting most of the components and gears required for the project. While this is a fairly dimensionally accurate process, it can lead to kerf which can change the dimensions of certain components. This could potentially lead to backlash in the gear system, which could make the overall finished product seem cheaper than an accurate and tight-fitting mechanism.

4 Comments. Leave new
This is really fascinating. I’m also working on a kinetic sculpture, but a much more simplistic approach. I respect your ambition and I hope it turns out how you hope. Can’t wait to see it. Good luck!
Hi Micheal, thank you! I am realizing it is potentially more ambitious than I had even initially thought, but I have ended up paring down the scope and focusing on the escapement mechanism instead of an organic kinetic sculpture. Good luck with your sculpture as well!
This is a large project you have undertaken, with many moving parts which will allow you to go many different directions with your aesthetic choices and more easily allow for mid-project design changes, as opposed to a single-part artifact which might present different manufacturing concerns. I agree that time might be a constraint for this project, especially given the requisite planning in CAD, but once you have a proper model, that should ease the manufacturing process. I especially like the antique wooden style you’ve chosen and I am excited to see where you go with this project!
Hi Nate, thank you! I am realizing the ambition of the project, but as you mentioned I am enjoying the flexibility that it is offering me. I think that assembly will be time consuming, as well will some initial testing. So far, I have spent quite a large amount of time working on and refining the CAD to get it somewhere I am happy with!