Completion finally feels like it is within reach. All the steel has been cut, excluding two saw cuts that will be fit a special way after the triangle comes together. My carbon process has been proven, though I intend to iterate it all the way until the end. The heat treating process for coloration is predictable. I think the jigs for attaching all the tubes are done. Small things always come up.
Currently, my carbon fiber tubing exceeds my expectations. While I have plans to make it even lighter, I would like to share the current Instron test results.
Under axial compression, the tubing withstands up to 8700 lbs. That’s fine with me. After yielding, it still withstands 8000. It does not spontaneously crack. Similarly under indentation, ultimate yield is 1720 lbs, however even post yield, it continues to hold 980 lbs. For whatever reason, my carbon does not fail in an explosion like everyone said it would. Maybe it’s because I followed manufacturer guidelines. Maybe I’m lucky.
As far as what hasn’t been done goes, I haven’t verified my carbon to steel adhesive. Because it is tubes inside tubes, my main interest is shear strength. The epoxy/polyamide compound I got is called “loctite e120hp hysol,” and is rated for 4000-4500 PSI. This means my weakest joint should still be 16000 pounds in tension at the weakest. Because full coverage of each joint is likely to be impossible, I’ve decided I’m willing to live with 6000 lbs. This test fixture nonetheless is currently curing and I’ll squish it on the Instron tomorrow.
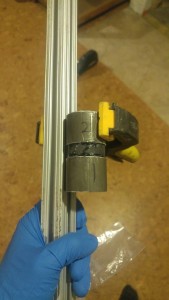
The tubes have also not all been combined. I have a few pictures to show you all, both of setup and product.
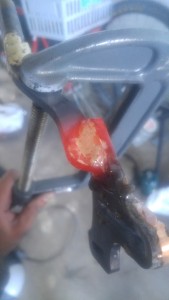
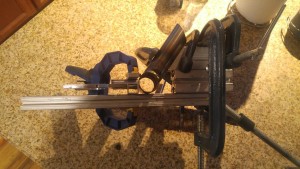
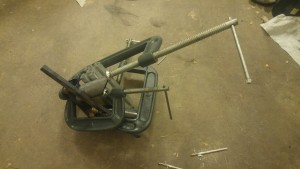
3 Comments. Leave new
I’d be worried about the stress risers on the carbon immediately after leaving the lug on the tube, given significant deformation that corner contact would bear the brunt of the load. Maybe consider some cantilever calculations. I’m happy you’re doing both the design analysis and checking it post manufacturing. I’m surprised the test results concluded tensile stress so high. How might you ensure all tubes meet these numbers?
You have really made this an incredible project! I agree with Sreyas that all of your manufacturing and aesthetic considerations are quite captivating.
What is your backup plan if the epoxy/polyamide compound doesn’t behave as expected for some reason (hope that doesn’t jynx anything) – will it be easy to switch to a different epoxy for all desired connections?
I can’t wait to see this thing at expo!
I am totally captivated by this project. The attention to detail is incredible – everything from manufacturing processes, to material properties, to aesthetic consideration. Really, really, impressive. I’m especially impressed with your use of destructive testing to verify your carbon fiber manufacturing methods. If you wanted to continue improving your manufacturing methods, do you think that your destructive tests pinpoint specific changes that need to be made to the process? Also, I know it’s not a direct failure mode of your tube, but maybe you should consider a torsion test in there too. With that, you’d be able to define a full stress tensor for your material.
Keep it up man.